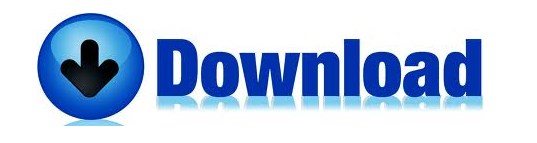
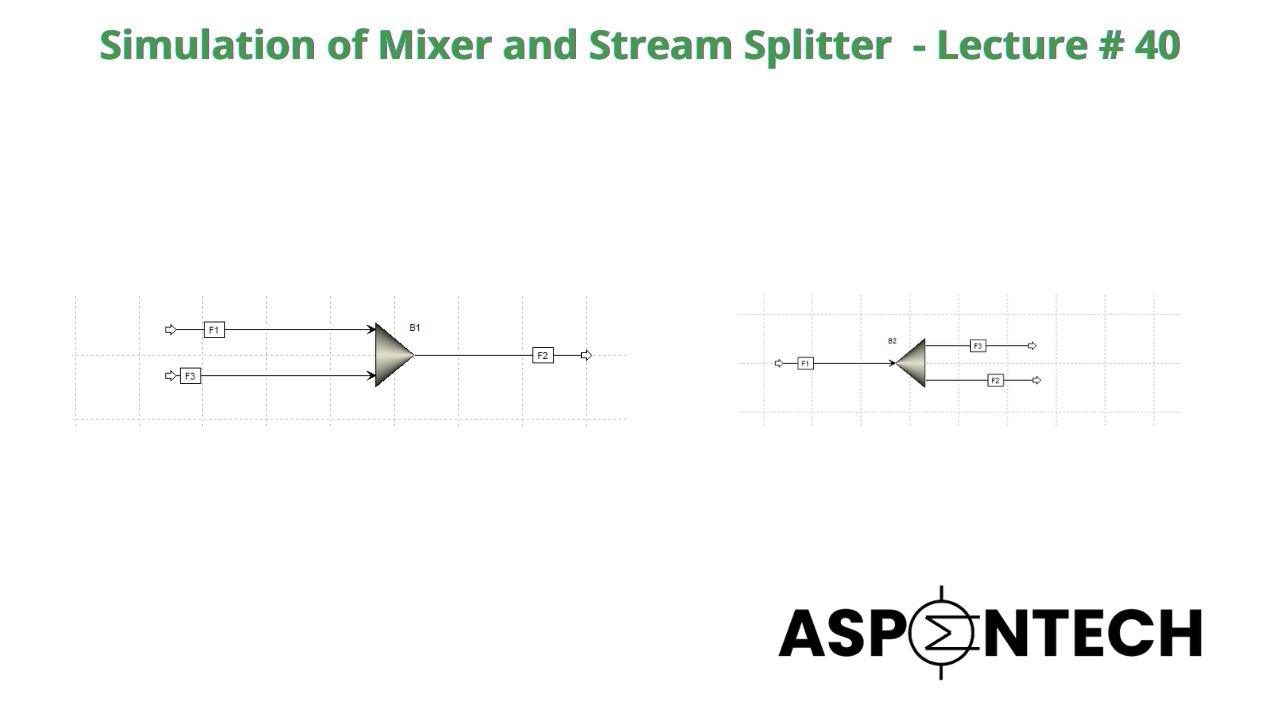
- #Combined heat and power simulation on aspen hysys free#
- #Combined heat and power simulation on aspen hysys crack#

Finally, the cost of the syngas for power generation, cooling, and heating was calculated. Moreover, the simulated syngas heat values were applied to a TFRJ3K straw gas engine. Second, syngas was passed to the reactor in Aspen Plus, which simulated the calorific values of the syngas produced by biomass pyrolysis under different conditions.

In the experiment, the yields of the gas before and after the addition of a catalyst were compared. First, syngas was used as a fuel source for the CCHP system, which can be produced through a biomass pyrolysis experiment. To achieve a higher energy efficiency and more cost-effective operation, a simplified cost analysis method based on the Advanced System for Process Engineering (Aspen Plus) was applied to the CCHP system based on biomass pyrolysis. Integrating combined CCHP systems with biomass pyrolysis results in a sustainable distributed energy system that effectively utilizes biomass resources and improves energy efficiency. Syngas is used directly as fuel source for the cooling, heating, and power (CCHP) system, which can be produced through biomass pyrolysis process. Ni-based catalysts supported on olivine were synthesized for cracking the biomass and producing the syngas. " Simulation and testing of the calorific value and cost analysis of biomass pyrolysis for heating, cooling, and power production," BioRes. In all, the waste plastic power plant generated a net power of 216.461KW at an equivalence ratio of 1.5.Zhang, K., Shi, X., Xin, X., Chen, K., Li, J., He, W., Qin, Z., Yang, H., and Zhang, C. To achieve proper energy optimization, the high temperature flue gas obtained from the gas turbine after pressure loss was passed through a “Heat Recovery Steam Generator” that allowed water at 25☌ to be heated up to produce steam which in turn drove a steam turbine to generate electricity of 255.3KW. In this reactor, the gaseous fuel burned with excess air in the combustion chamber to produce a high temperature and pressured gas that drove the gas turbine (modelled as an expander) to generate electrical power of 1194KW.
#Combined heat and power simulation on aspen hysys free#
After cooling of the top product and separation to obtain the volatile gaseous fuel from the liquid fuel oil, the volatile gaseous fuel alongside air were pressurized with a compressor and then combusted in a Gibbs free energy reactor.
#Combined heat and power simulation on aspen hysys crack#
The pyrolysis reactor modelled as a conversion reactor was used to thermally crack 2000Kg/h of HDPE feed at a temperature of 450☌ to produce a top product containing a mixture of liquid fuel oil and volatile gaseous fuel. A simulation model that produces electricity from the High Density Polyethylene (HDPE) waste plastics has been developed using Aspen Hysys process simulator. This paper presents a theoretical framework for the simulation of waste plastic power plant. Where recycling becomes an issue, technologies that utilize the waste plastics to generate electricity can be employed. Non-recyclable plastic materials are used in areas like packaging, 3D printing, and construction. The recovery of this abundant energy helps to curb environmental concerns associated with plastic utilization. The high energy content of plastics can be converted to electricity.
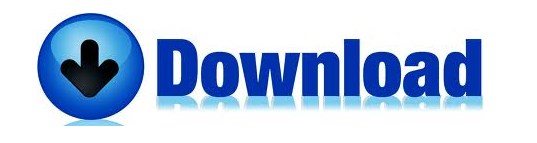